Measured backpressure on stock turbo
#16
EvoM Guru
iTrader: (50)
Did a quick test on turbine pressure relative to charge pressure for those curious about backpressure on small turbo's.
Setup: VIII turbo with 10.5 HS, stock WGA with about 5psi preload over stock, stock cam gear settings, methanol injection, MBC, stock exhaust manifold and O2 housing, stock intake manifold, IC and charge assembly, temperature about 75 degrees.
compressor psi / turbine psi
Pressure was obtained by tapping into egr valve hotside and readings were taken from a pressure guage.
Eventually I will do the same test with delayed intake valve openening
Setup: VIII turbo with 10.5 HS, stock WGA with about 5psi preload over stock, stock cam gear settings, methanol injection, MBC, stock exhaust manifold and O2 housing, stock intake manifold, IC and charge assembly, temperature about 75 degrees.
compressor psi / turbine psi
10 / 10 (3700 rpm)
20 / 20
25 / 35
30 / 40 (4500 rpm)
28 / 42
27 / 45
26 / 48 (7000 rpm)
Rpm data is crude relative to pressure differences. Pressure will peak at 48 psi I believe due to pressure induced WG relief.20 / 20
25 / 35
30 / 40 (4500 rpm)
28 / 42
27 / 45
26 / 48 (7000 rpm)
Pressure was obtained by tapping into egr valve hotside and readings were taken from a pressure guage.
Eventually I will do the same test with delayed intake valve openening
#18
Looks like my only option is to get a turbo system that makes power, not yet.
Still 3 minor things that may help (ported jet housing, delay int valve and/or adv exh, or even clip the turbine blades)
Anyone know if the Bushurracing ported turbine housing will open this up? I could care less about spool, all that does is waste rubber and clutch material.
Still 3 minor things that may help (ported jet housing, delay int valve and/or adv exh, or even clip the turbine blades)
Anyone know if the Bushurracing ported turbine housing will open this up? I could care less about spool, all that does is waste rubber and clutch material.
#21
Evolved Member
iTrader: (8)
If I recall correctly, the turbine flow maps are based on corrected mass flow rate.
I could be completely off here, but I believe a flat line on the turbine flow map actually means that the turbo is in a range of linearity where as exhaust back pressure pre-turbo goes up exhaust flow increases in a linear manner. Maybe somebody with more knowledge can confirm or correct this though, as it's been quite a while since I've looked at the turbine mass flow rate correction equation and I can't seem to find it now.
The limiting factor becomes engine volumetric efficiency. As boost goes up, exhaust back pressure rises quicker then intake pressure (but in a linear manner) and engine VE drops off due to the back pressure. Using a larger turbine housing increases the amount of airflow for a given pressure ratio, there by reducing the back pressure gain and allowing the engine VE to remain higher.
I also agree that larger wastegates will do almost nothing to lower back pressure. The turbo NEEDS a certain amount of back pressure and heat to sustain the turbocharger shaft velocity to produce the required energy needed to compress the charge air. A larger wastegate just means it will open less because it still needs the same back pressure to obtain the desired boost level. I think some of the fastest domestic drag cars actually run without wastegates and instead use pop off valves to prevent damaging boost spikes.
I could be completely off here, but I believe a flat line on the turbine flow map actually means that the turbo is in a range of linearity where as exhaust back pressure pre-turbo goes up exhaust flow increases in a linear manner. Maybe somebody with more knowledge can confirm or correct this though, as it's been quite a while since I've looked at the turbine mass flow rate correction equation and I can't seem to find it now.
The limiting factor becomes engine volumetric efficiency. As boost goes up, exhaust back pressure rises quicker then intake pressure (but in a linear manner) and engine VE drops off due to the back pressure. Using a larger turbine housing increases the amount of airflow for a given pressure ratio, there by reducing the back pressure gain and allowing the engine VE to remain higher.
I also agree that larger wastegates will do almost nothing to lower back pressure. The turbo NEEDS a certain amount of back pressure and heat to sustain the turbocharger shaft velocity to produce the required energy needed to compress the charge air. A larger wastegate just means it will open less because it still needs the same back pressure to obtain the desired boost level. I think some of the fastest domestic drag cars actually run without wastegates and instead use pop off valves to prevent damaging boost spikes.
#22
Evolving Member
iTrader: (4)
If I recall correctly, the turbine flow maps are based on corrected mass flow rate.
I could be completely off here, but I believe a flat line on the turbine flow map actually means that the turbo is in a range of linearity where as exhaust back pressure pre-turbo goes up exhaust flow increases in a linear manner. Maybe somebody with more knowledge can confirm or correct this though, as it's been quite a while since I've looked at the turbine mass flow rate correction equation and I can't seem to find it now.
I could be completely off here, but I believe a flat line on the turbine flow map actually means that the turbo is in a range of linearity where as exhaust back pressure pre-turbo goes up exhaust flow increases in a linear manner. Maybe somebody with more knowledge can confirm or correct this though, as it's been quite a while since I've looked at the turbine mass flow rate correction equation and I can't seem to find it now.
Anyone know the answer to this? Just looking at a map it seems like at a certain point more backpressure doesn't spin the turbine any faster, so you could bleed it off to increase VE. Isn't that what variable vane turbines were designed to do basically? And how high does the pressure ratio get on small turbos running max boost?
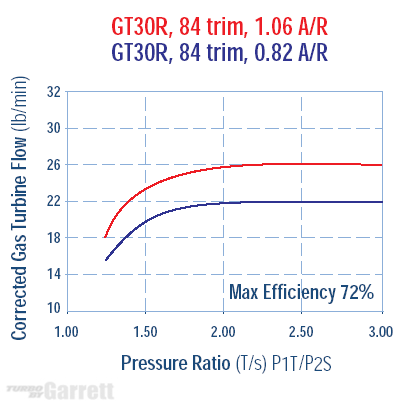
#23
Evolving Member
iTrader: (8)
Join Date: Mar 2006
Location: in a van down by the river
Posts: 240
Likes: 0
Received 0 Likes
on
0 Posts
Backpressure will increase as turbine pressure ratio (aka expansion ratio) increases.
Think about this in terms of the graph posted above, where the 0.82 turbine housing is swapped for the 1.06. In the simplest terms possible, the 1.06 doesn't need to wastegate as much flow as the 0.82. As a result the turbine can now generate its necessary shaft power using mass flow instead of pressure ratio.
Imagine a line of constant turbine power overlaid on the turbine map above. It would curve from the top left portion of the map, down sharply and the flatten out as it approaches the bottom right portion of the map. It would also intersect each of the two turbine flow curves. These two intersections dictate the corresponding pressure ratio and mass flow for each turbine (assuming same turbine efficiency) at this engine operating condition.
The difference in pressure ratio dictates the difference in backpressure between the two turbines. And the mass flow difference between these two intersections is the difference in the amount of wastegated flow for each turbine.
Think about this in terms of the graph posted above, where the 0.82 turbine housing is swapped for the 1.06. In the simplest terms possible, the 1.06 doesn't need to wastegate as much flow as the 0.82. As a result the turbine can now generate its necessary shaft power using mass flow instead of pressure ratio.
Imagine a line of constant turbine power overlaid on the turbine map above. It would curve from the top left portion of the map, down sharply and the flatten out as it approaches the bottom right portion of the map. It would also intersect each of the two turbine flow curves. These two intersections dictate the corresponding pressure ratio and mass flow for each turbine (assuming same turbine efficiency) at this engine operating condition.
The difference in pressure ratio dictates the difference in backpressure between the two turbines. And the mass flow difference between these two intersections is the difference in the amount of wastegated flow for each turbine.
#24
Evolving Member
iTrader: (8)
Join Date: Mar 2006
Location: in a van down by the river
Posts: 240
Likes: 0
Received 0 Likes
on
0 Posts
I also agree that larger wastegates will do almost nothing to lower back pressure. The turbo NEEDS a certain amount of back pressure and heat to sustain the turbocharger shaft velocity to produce the required energy needed to compress the charge air. A larger wastegate just means it will open less because it still needs the same back pressure to obtain the desired boost level. I think some of the fastest domestic drag cars actually run without wastegates and instead use pop off valves to prevent damaging boost spikes.
Some turbo drag cars will open the BOV while staging to increase the compressor's mass flow throughput in order to avoid compressor surge.
#25
Evolving Member
iTrader: (4)
I understand that a larger housing will require less wastegated flow to reach the same turbine power, because it takes more flow to get to a given pressure ratio. So the 1.06 housing is flowing more at a 2.0 ratio than the .82 housing.
What I'm getting at is the turbine doesn't flow any more at a 3.0 ratio than it does at a 2.0 ratio, so the backpressure is wasted and just hurting the engines VE. So if you were to wastegate the exess exhaust to keep the ratio at 2.0 you would increase engine VE without sacrificing turbine power (compressor speed).
In the end I'm wondering if it's worth it to wastegate some of the exhaust even if you are trying to keep the compressor at the highest possible rpm, and how much to let go - probably however much you can let go and still keep a 2.0 turbine pressure ratio
What I'm getting at is the turbine doesn't flow any more at a 3.0 ratio than it does at a 2.0 ratio, so the backpressure is wasted and just hurting the engines VE. So if you were to wastegate the exess exhaust to keep the ratio at 2.0 you would increase engine VE without sacrificing turbine power (compressor speed).
In the end I'm wondering if it's worth it to wastegate some of the exhaust even if you are trying to keep the compressor at the highest possible rpm, and how much to let go - probably however much you can let go and still keep a 2.0 turbine pressure ratio
#26
Evolved Member
iTrader: (8)
If you actually find a real turbine flow map, you will see there are shaft speed lines. That Garrett map is actually just a "median ranks" type of line. Below is a more engineering based turbine flow map.

You can see a few things in this chart:
1. The turbine flow rate is a corrected flow rate.
This means that pressure and temperature must be taken into account. These are "inlet" conditions, so the hotter your exhaust is and the lower inlet pressure there is (exhaust back pressure) the higher the corrected airflow is. My memory appears to have served me well and a flat line on a turbine flow map means a linear airflow relationship is obtained based on the pressure ratio across the turbine. In other words, more exhaust pressure means higher exhaust flow through the turbine, at the expense of lower engine volumetric efficiency caused by the increase in backpressure.
2. Shaft speed is depended on flow rate and pressure ratio. You can have the exact same shaft speed and have very different mass flow rate numbers and inlet pressures.
3. Turbine efficiency varies greatly at spool up, but approaches a nominal value at higher shaft speeds with very little dependency on pressure ratio and mass flow rate.

You can see a few things in this chart:
1. The turbine flow rate is a corrected flow rate.
This means that pressure and temperature must be taken into account. These are "inlet" conditions, so the hotter your exhaust is and the lower inlet pressure there is (exhaust back pressure) the higher the corrected airflow is. My memory appears to have served me well and a flat line on a turbine flow map means a linear airflow relationship is obtained based on the pressure ratio across the turbine. In other words, more exhaust pressure means higher exhaust flow through the turbine, at the expense of lower engine volumetric efficiency caused by the increase in backpressure.
2. Shaft speed is depended on flow rate and pressure ratio. You can have the exact same shaft speed and have very different mass flow rate numbers and inlet pressures.
3. Turbine efficiency varies greatly at spool up, but approaches a nominal value at higher shaft speeds with very little dependency on pressure ratio and mass flow rate.
#28
Evolving Member
iTrader: (8)
Join Date: Mar 2006
Location: in a van down by the river
Posts: 240
Likes: 0
Received 0 Likes
on
0 Posts
If you actually find a real turbine flow map, you will see there are shaft speed lines. That Garrett map is actually just a "median ranks" type of line. Below is a more engineering based turbine flow map.

You can see a few things in this chart:
1. The turbine flow rate is a corrected flow rate.
This means that pressure and temperature must be taken into account. These are "inlet" conditions, so the hotter your exhaust is and the lower inlet pressure there is (exhaust back pressure) the higher the corrected airflow is. My memory appears to have served me well and a flat line on a turbine flow map means a linear airflow relationship is obtained based on the pressure ratio across the turbine. In other words, more exhaust pressure means higher exhaust flow through the turbine, at the expense of lower engine volumetric efficiency caused by the increase in backpressure.
2. Shaft speed is depended on flow rate and pressure ratio. You can have the exact same shaft speed and have very different mass flow rate numbers and inlet pressures.
3. Turbine efficiency varies greatly at spool up, but approaches a nominal value at higher shaft speeds with very little dependency on pressure ratio and mass flow rate.

You can see a few things in this chart:
1. The turbine flow rate is a corrected flow rate.
This means that pressure and temperature must be taken into account. These are "inlet" conditions, so the hotter your exhaust is and the lower inlet pressure there is (exhaust back pressure) the higher the corrected airflow is. My memory appears to have served me well and a flat line on a turbine flow map means a linear airflow relationship is obtained based on the pressure ratio across the turbine. In other words, more exhaust pressure means higher exhaust flow through the turbine, at the expense of lower engine volumetric efficiency caused by the increase in backpressure.
2. Shaft speed is depended on flow rate and pressure ratio. You can have the exact same shaft speed and have very different mass flow rate numbers and inlet pressures.
3. Turbine efficiency varies greatly at spool up, but approaches a nominal value at higher shaft speeds with very little dependency on pressure ratio and mass flow rate.
These operating conditions can (and often do) dictate that the turbine is operating on speedline regions that are not shown on its map. Imagine the tails of all those parabolic speed lines extrapolated in both directions. The turbine can operate there.
Take for example the case of a oversized compressor wheel with a "too small" turbine wheel. For a given engine (and hence compressor) operating point, the turbine is forced to deliver the required shaft power to drive the compressor at a relatively slow rotational speed. As a result, the turbine operates on a portion of a speedline that is way off peak efficiency.
Extending this example to the map above, the turbine could very well be operating at 120krpm and 2.0 pressure ratio. As you might guess, the efficiency at this point is quite low, which adversely affects its ability to generate power. This is turn affects the turbine pressure ratio required to provide the shaft power, and so on.
It is iterative and converges when you have speed, mass flow, and power balance between the compressor and turbine for a given engine operating point.
#29
Evolved Member
iTrader: (8)

Yep
Now we are getting beyond normal forum talk though, people are tuning out and those interested either already know or can figure it out on their own through other resources.
Your post does point out the importance of a proper turbine match, something I feel that is often over looked and under emphasized. I'd rather have a sick turbine with a good match to a poor compressor wheel, then the sickest compressor wheel out there bolted onto a crappy, poorly matched turbine.
The bad part about all of this is that us high altitude guys experience combinations that match differently then at sea level. Makes things interesting when selecting a turbo as a turbo that may perform well at sea level might not work so hot up here.
#30
I delayed intake valve 2 degrees (fixed) and removed additional WGA preload with no boost controlling hookup (except a failsafe signal from WM sys or knock patch). So turbine backpressure dictates itself. Boost is lower at peak 26 - 29 (depending on gear) and will drop about 3-4 psi at higher rpm.
Delaying the Int cam definately picked up the rpm slope up top where it would fall before with no significant change at peak. This is with less boost.
I couldn't say if the results would be the same without additional cooling from WM, like with racing fuel, but it worked in my case.
Delaying the Int cam definately picked up the rpm slope up top where it would fall before with no significant change at peak. This is with less boost.
I couldn't say if the results would be the same without additional cooling from WM, like with racing fuel, but it worked in my case.