EVO 8 Guru Question!! Front subframe not happy!! ; [
#17
Newbie
iTrader: (1)
Join Date: Aug 2012
Location: Seattle
Posts: 35
Likes: 0
Received 0 Likes
on
0 Posts
OK, here's the pic.
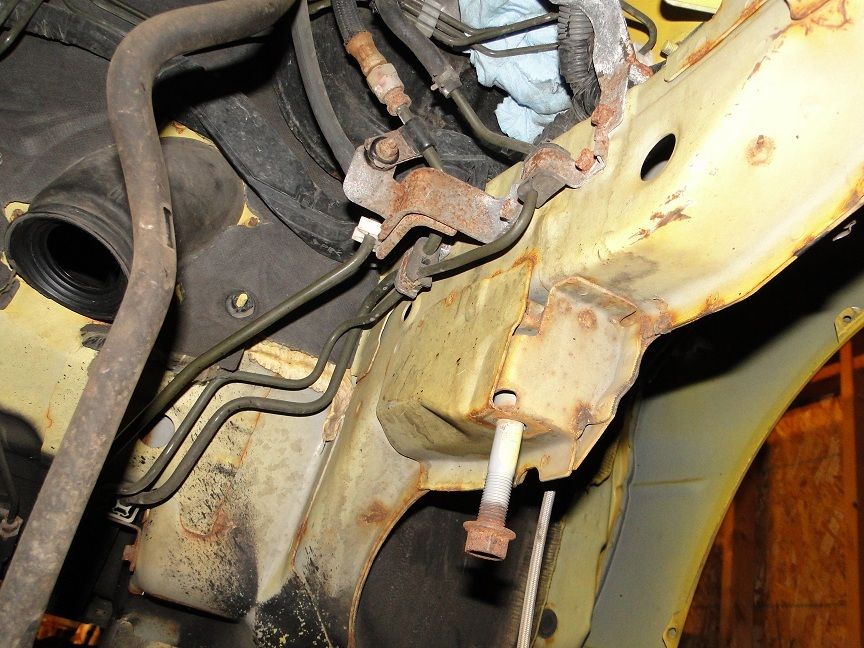
Unfortunately, there is no part number for this. It comes with an entire sideframe assembly, which is the entire fender that connects to the main chassis. Only suggestion I can give you is to weld the subframe to the chassis/sideframe. Of course, the stud will still wiggle around so just spot weld it in place and you should be fine.
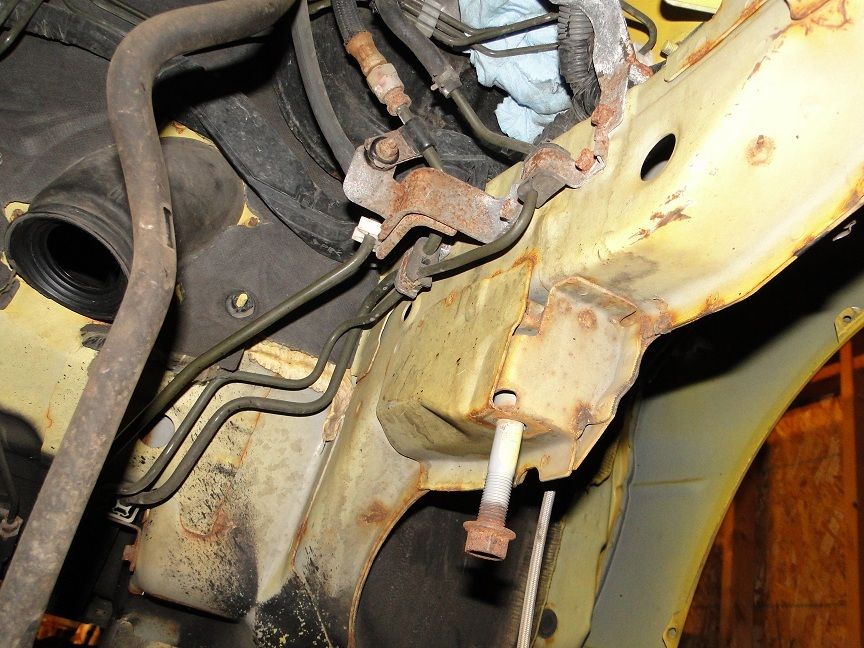
Unfortunately, there is no part number for this. It comes with an entire sideframe assembly, which is the entire fender that connects to the main chassis. Only suggestion I can give you is to weld the subframe to the chassis/sideframe. Of course, the stud will still wiggle around so just spot weld it in place and you should be fine.
#18

WTF you cant be serious? you want him to weld the subframe to the car? thats absurd. what i would do and have done in the past to a captured bolt is weld the "bolt" stud to the chassis to prevent it from spinning. lucky for you with this particular stud you dont need to cut an access hole. just take a wire wheel and clean off that hole that is exposing the top of the stud and weld it as best as possible. let me know if i can help any further.

An access hole is what I want to do, it would be the best way, and that is what I planned on doing from the beginning, I am curious how it came undone in the frame rail,

What I want to do is, take the required items out of the engine way, create a access port to the stud, clean it up best I can, and weld it, weld up the access port, prime it was etching primer, and paint + clear it. I hope this will take care of the issue, what bothers me though, is the fact the nut is on this, so did it get damaged and can't be tightened anymore?
If you have any other suggestions let me know, I wish it was a bolt and not a stud! ha..
#19
Evolved Member
iTrader: (23)
WTF you cant be serious? you want him to weld the subframe to the car? thats absurd. what i would do and have done in the past to a captured bolt is weld the "bolt" stud to the chassis to prevent it from spinning. lucky for you with this particular stud you dont need to cut an access hole. just take a wire wheel and clean off that hole that is exposing the top of the stud and weld it as best as possible. let me know if i can help any further.
#25
Evolved Member
iTrader: (25)
It broke because its a "weld nut" it only has a few sections which are actually welded to the frame, its not welded all the way around, this is very common. I have actually seen them break before on other vehicles.
What I would do... Drill like 10-12 small holes around the nut's outer diameter, and basically use rosset type welds to secure it back in place and than grind/sand it flat. That should hold no problem if done correctly.
What I would do... Drill like 10-12 small holes around the nut's outer diameter, and basically use rosset type welds to secure it back in place and than grind/sand it flat. That should hold no problem if done correctly.
#26
It broke because its a "weld nut" it only has a few sections which are actually welded to the frame, its not welded all the way around, this is very common. I have actually seen them break before on other vehicles.
What I would do... Drill like 10-12 small holes around the nut's outer diameter, and basically use rosset type welds to secure it back in place and than grind/sand it flat. That should hold no problem if done correctly.
What I would do... Drill like 10-12 small holes around the nut's outer diameter, and basically use rosset type welds to secure it back in place and than grind/sand it flat. That should hold no problem if done correctly.
#27
Evolved Member
iTrader: (25)
10 or 12 small access holes? What I was thinking of doing was removing the fender and inner fender on the driver side, and gaining access that way. I would not have to remove any parts from the engine bay, and I would have a lot more room, I guess we will see, your idea can you explain it a little more, and you say maybe that weld nut is tacked like 4 times you think/ Mitsubishi welds break easy from what I have seen in the past if they do it like that still.
I made this attachment for you, basically you drill holes around the nut getting as close to it as possible, then high heat mig weld the hole closed and draw the weld pool into the nut. Do this 8 times evenly and it will secure the nut no problem. Then clean/sand/grind the bearing surface the subframe bolts too on the frame.
... is this the best way? I dunno

Keep in mind you'll have to find some way to secure the nut by bolting something to it as you place the first few welds, making sure the nut is level is important.
Hope that helps
-Joe
Last edited by GTijoejoe; Oct 4, 2012 at 07:12 PM.
#28

Sure thing, you could probably get away with 8 holes.... A weld nut is 'projection welded', they have these small tangs on the end of the nut which basically get fused into the sheet you are welding to.
I made this attachment for you, basically you drill holes around the nut getting as close to it as possible, then high heat mig weld the hole closed and draw the weld pool into the nut. Do this 8 times evenly and it will secure the nut no problem. Then clean/sand/grind the bearing surface the subframe bolts too on the frame.
... is this the best way? I dunno
but its exactly what I would do if I were in your position opposed to cutting holes in the side of the frame or something silly like that to gain access to the top of the nut. If you can't weld it evenly side to side, it will distort the nut.
Keep in mind you'll have to find some way to secure the nut by bolting something to it as you place the first few welds, making sure the nut is level is important.
Hope that helps
-Joe
I made this attachment for you, basically you drill holes around the nut getting as close to it as possible, then high heat mig weld the hole closed and draw the weld pool into the nut. Do this 8 times evenly and it will secure the nut no problem. Then clean/sand/grind the bearing surface the subframe bolts too on the frame.
... is this the best way? I dunno

Keep in mind you'll have to find some way to secure the nut by bolting something to it as you place the first few welds, making sure the nut is level is important.
Hope that helps
-Joe
That makes sense drilling the holes so I can puddle it up, so I do not distort the nut.
#29
Evolving Member
iTrader: (10)
Join Date: Apr 2007
Location: Kansas/Oklahoma
Posts: 249
Likes: 0
Received 0 Likes
on
0 Posts
I don't know why everyone is trying to make this so complicated. You can clearly see the top of the bolt through the corner of the plate. If you just turned the heat up and put a ground on the bolt and welded the **** out of the bolt building it up and attaching it to the frame on both sides and it will be solid. Yes I agree drilling holes would work but I don't think its necessary. Just my opinion.
#30
Evolving Member
iTrader: (10)
Join Date: Apr 2007
Location: Kansas/Oklahoma
Posts: 249
Likes: 0
Received 0 Likes
on
0 Posts
2nd thought that would be even easier. IF you have access to an air ratchet. Wedge a big screw driver/pry bar in between the nut and the sub frame putting tension on the bolt. Then crank on it with the air ratchet. Sometimes that is enough to let the nut start moving up. Once there is tension on the bolt and the frame the tighter the nut gets the more tension is on the bolt and you should be able to get it tightened up. This might or might not work but I have done it in several different scenarios.